choice of treatment: the need for an evaluation
Reading time:The elements constituting this global approach are part of a response to regulatory requirements and in particular, those of the ministerial decrees of December 14, 2013 relating to the prevention of the Legionella risk (France).
A global approach is necessary in order to establish and implement a specific programme, which can be adapted to environmental evolutions, so that the use of a given water in given conditions does not penalise the industrial production for which this water is used.
This approach is based on a regular assessment of performances objectives and lines for progress are defined whilst integrating technological and regulatory evolutions.
This global approach is essential as limiting the impact of water use does not amount to the simple addition of chemical products. In effect, water use has an impact on the following aspects:
- the efficiency of the system’s heat exchangers, energy costs;
- the water consumption and the associated costs (sampling conditioning, blowdowns);
- the time of team mobilisation, management of work time, reactivity;
- the level of technical expertise, training and communication;
- respect for regulatory requirements;
- human health;
- the environment;
- safety.
All of these points should be considered in the study to determine which monitoring has to be implemented. In the same way as prevention tools such as FMECA (Failure Modes, Effects and Criticality Analysis), HAZOP (Hazard and Operability studies), HACCP (Hazard Analysis Critical Control Point), this global approach is both adaptable and open to criticism, in order for choices to be called into question and evolve.
the evaluation
The evaluation is an initiative which aims to understand in which conditions the water will be used and which tools are the best adapted to prevent or limit the consequences linked to the use of this particular water in given conditions. This approach highlights:
- the characteristics of the circuit :
- dead points – portions which are unused or only used intermittently, frequency of use;
- temperature;
- equipment type;
- volumes and residence times;
- condition of surfaces;
- shutdowns – cleaning / disinfection – start-ups.
- qualities of water available to supply circuits;
- the cooling tower’s operating mode(s);
- the product, water, matter report;
- the analytical characteristics of water - as a minimum for make-up water and circuit water, analyses of all the parameters relating to scaling, corrosion and / or bio-fouling:
- micro-biological report (counting via ACBF culture (Aerobic Cultivable Bacterial Flora; Counting total bacterial flora with an epi-fluorescence microscope; Counting bacterial DNA by Polymerase Chain Replication);
- physicochemical report ( pH , conductivity – alkaline strength (p-alkalinity) and total alkali strength (m-alkalinity) - total hardness (TH), calcium hardness (THca)– Ammonium, Nitrates, Nitrites – Sulphates, Sulphites –- Iron, Copper, Zinc, - Chlorides – Suspended Solids - TOC -COD).
The evaluation results in:
- the definition of a monitoring programme;
- the choice of equipment, technologies, formulations which will respect the economic, regulatory, environmental and performance constraints. The injection point is chosen to maximise the distribution of the product in the water, and ensure a sufficient product action at an adapted dose and contact time. The environmental impact of the blowdown must be included in the treatment definition;
- objectives to be reached and the processing of data and events per fixed period;
- the impact of the frequency of monitoring which is expressed in the graph. It is important to adapt the frequency of monitoring to the variability of the parameter considered. If this is not the case, drifts, which may have more or less serious consequences, may not be detected.
Monitoring is the control panel for preventive action and allows reporting within the context of regulatory obligations.
reports
- cooling tower operating report;
- matter report: water produced to check that the doses injected comply with instructions;
- microbiological and physicochemical report for the parameters selected;
- the relevant parameters resulting from the evaluation in relation to the potential problems owing to the quality of make-up water and conditions of use. Limit values will be defined for every indicator;
- frequency dependent on the variability of the parameter considered and its impact on bacterial growth;
- real-time monitoring of the residual reagent via a specific probe and data logger, by spectrophotometric dosing;
- use of results to adjust and justify treatment doses;
- checks on injection equipment and automation (remote monitoring).

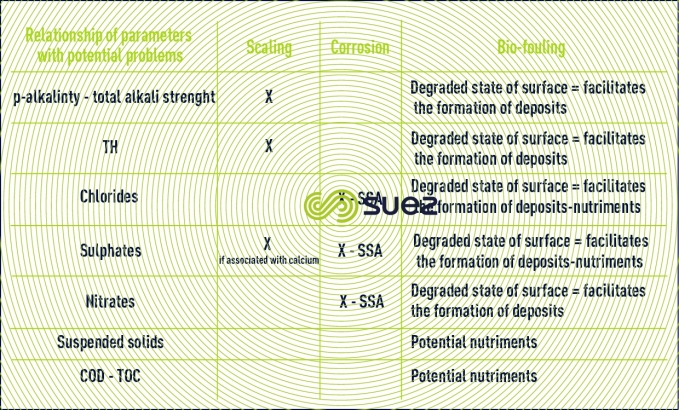

corrosion monitoring
The corrosion phenomenon can be continuously monitored on site in two different ways:
- via weight loss on test coupons;
- via a measuring probe, Corrater probe type.
The first will be more accurate, but will give a value over a long period of time; individual events are not highlighted. The second gives the real-time value allowing events to be assessed, or dosing or operating conditions to be fine-tuned (blowdown flow, concentration ratio).
Electrochemical probes permit instantaneous corrosion rate measures to be obtained and transmitted to the aqualead® access data acquisition system.

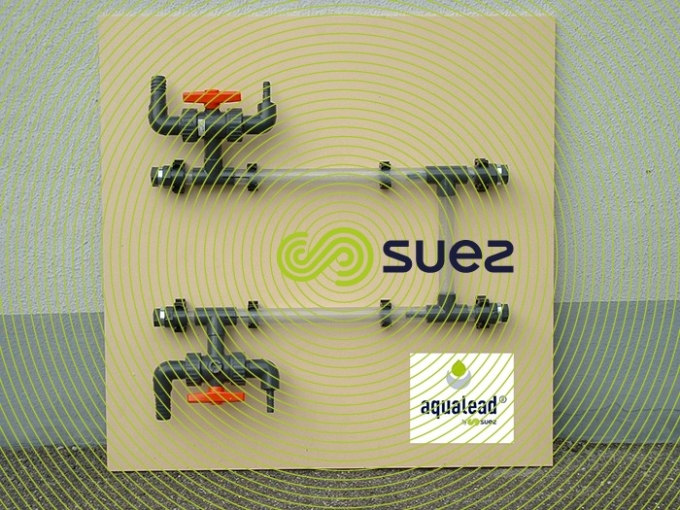


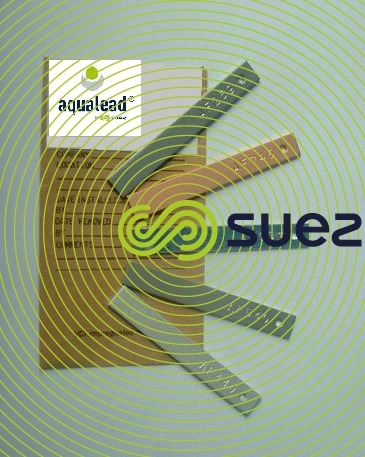


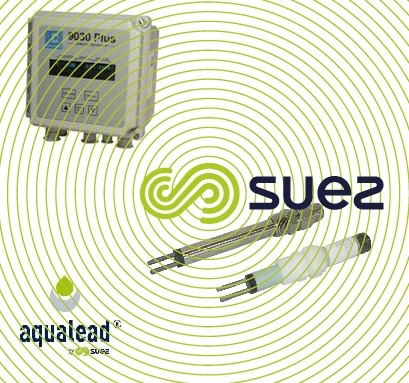

risk analysis
A methodical risk analysis of the proliferation and dispersion of Legionella in cooling towers where water is dispersed into an air flow is based on a HAZOP (Hazard and Operability studies), FMECA (Failure Modes, Effects and Criticality Analysis), HACCP (Hazard Analysis Critical Control Point) type methodology. It consists in identifying all of the risk factors present in the system, their environment and the means of limiting, controlling or eradicating these risks.
The analysis will include all of the elements likely to influence:
- the bacterial contamination of equipment;
- bacterial proliferation;
- dissemination of Legionella into the atmosphere.
training
Well-trained personnel will be more operational, efficient and pro-active. Their contribution towards the prevention initiative will consequently be both more often and more effective.
In this case, it consists in technical training programmes dedicated to water conditioning activities. The objective is to improve the knowledge of industrial contacts and operators in the following domains:
- technical, scientific and regulatory aspects;
- cooling towers management and cost control;
- health, safety and the environment to optimise the prevention initiative and QHSE (Quality Health Security Environment). approach.
As these training programmes do not result in a diploma or certificate being obtained, it is important to solicit a body possessing a registration number, proposing several specific training modules and capable of providing basic training enabling a good level of expertise to be acquired.
It is also recommended to properly define needs to ensure that an individual adapted programme can be proposed.
pilot facilities
In addition to innovation-related aspects, a pilot unit can contribute towards conducting tests without any risks for the industrial facility. It will be possible to assess the performances of the various conditioning programmes, to determine the best choices of formulations in given operating conditions.
Consequently, it will be possible to:
- test new products once they have been developed by a laboratory;
- compare the effectiveness of products against scaling and corrosion;
- find the best solution to a specific water conditioning problem.
Pilot units are very flexible technical tools which enable:
- make-up water to be synthesized or site water to be used;
- the conditions encountered on semi-open circuits to be simulated;
- turbidity, conductivity, pH, corrosion and heat exchanges to be monitored;
- the most effective product to be chosen according to the problems encountered on the site and reproduced at the pilot unit.
The design of the pilot unit can make it a “fixed” tool associated with a laboratory or a mobile unit which can be used on site.
The advantages of the mobile unit are:
- to optimise technical solutions on site whilst using the site’s water without plant modification;
- to check the effectiveness of products before embarking on an industrial trial.
storage and injection equipment
Conditioning, storage conditions, the implementation of formulations and their “handling”, all have an impact on Health, Safety and the Environment.
It is for this reason that this topic must be studied beforehand in order to minimise the impacts and the costs and anticipate communication and information required.
Furthermore, regulatory obligations exist and must be satisfied, in particular as regards preventing chemical risks which must be included in the user company’s global risk document.
Among the existing means, it is recommended, where possible, to use dedicated, identified “bulk” airtight storage units which include:
- volume measurement (consumed - residual);
- the dosing station;
- a product transfer / offloading system;
- a connection to monitoring equipment;
- information on the products and implementation conditions including PPE (Personal Protective Equipment);
The advantages of this type of unit:
- chemical risk prevention:
- less exposure to chemical products, chemical product handling minimised;
- limited risks of accidental spillage;
- foregoes the need to manage empty packaging;
- consumption management optimisation:
- checks on levels;
- products which have been paid for are no longer thrown away (empty packaging can contain between 1 and 5% of the volume initially contained);
- centralisation of the storage zone.
Once the storage unit installed on site, chemical products are directly delivered and offloaded. This operation is supervised by a trained and qualified operator.

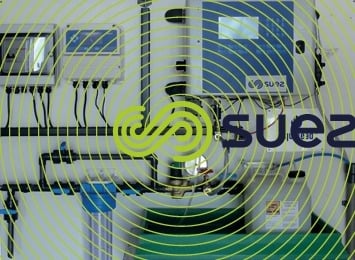

real-time KPI monitoring: aqualead® access
Analysers allow a given parameter to be checked more frequently or continuously if necessary. The principle is based on a colorimetric measure, or a global or specific electrochemical potential (redox) or a measurement of fluorescence. Certain ‘families” of analysers such as chlorine dosing systems can use either of these technologies .The measurement taken can be transmitted to a central control with the objective of:
- adjusting the functioning of dosing pumps;
- putting in place alarms;
- transmitting information and remotely managing a situation;
- compiling numerous data records facilitating the correspondence with the evolution of other parameters or certain events.

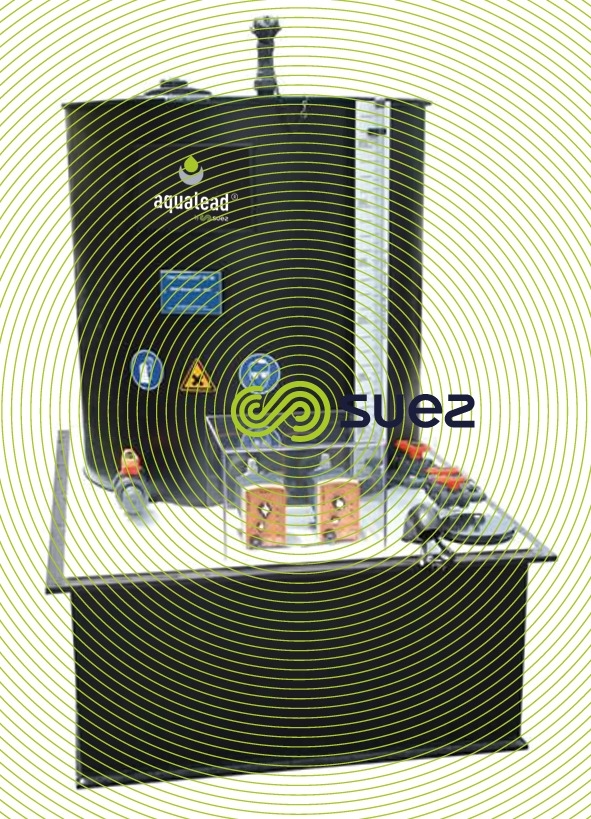

checking dosing by measuring fluorescence
This technology is based on the integration of a fluorescent marker in the formulations used. It consists of continuous measurement of the concentration of the marker in water by an analyser which ensures a stable dosage and adjustments in real-time.
This permanent adjustment of doses enables:
- the cost and quality of blowdowns to be optimised;
- conditioning to be permanently adapted to the hazards of cooling towers operation.
Continuous analysis significantly reduces the number of “manual” analyses to be performed during the year, as well as reagent discharge.
Over time, the stabilisation of formulation injections leads to a better protection of cooling towers and optimises the sustainability of surface conditions.
other online analysers
Numerous other analysers exist which allow to manage equipment, including dosage and blowdowns.
- corrosion measurement;
- conductivity meter;
- pH meter;
- phosphate meter;
- total alkali strength meter;
- …
These analysers are chosen at the time of the evaluation according to the KPI selected.

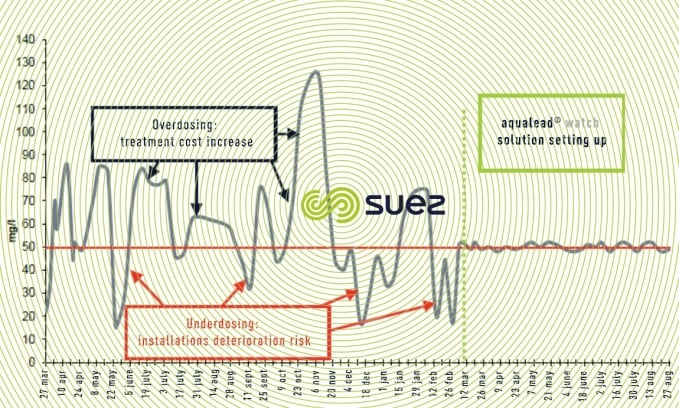

Bookmark tool
Click on the bookmark tool, highlight the last read paragraph to continue your reading later
